About The Car

Design philosophy
In the Greenpower challenge all the competitors have a uniform motor and batteries. As everyone is working with the same power plant the race is won by producing the most efficient car possible. The key areas affecting the design are therefore aerodynamics, rolling resistance and drive train efficiency.
Initial Development
The design process commenced with a look into some motorsport design classics; this was done to trigger some inspiration to help in the creation of a range of original concepts. F1 has always been at the pinnacle of motorsport and the forefront of technological development so it was the ideal place to start when looking for ideas that could be applied to our racer.
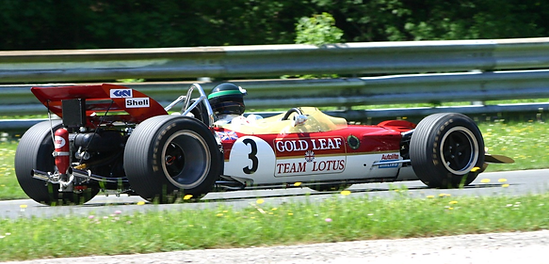
In the early days of F1 there were few limitations and teams could design freely for speed and traction, this lead to highly efficient designs. One of the most iconic designs from the early years was Lotus's 1969 car, certain aspects of the Lotus would be ideal for use on our racer; it is a relatively uncomplicated shape which would make the manufacture of the bodywork much simpler, in addition a long/thin body is a characteristic that has excelled at green power in the past.
Coincidently the 69’ lotus pictured was actually sponsored by GKN.
Initial Concept
Our initial design bore a lot of similarities to the Lotus, with a long thin body and exposed wheels.
The design has a relatively long wheel base to lower the driving position, this reduces the height of the vehicle making it more aerodynamically efficient.
The Greenpower races are all about maintaining the highest speed possible at all times, with wide corners and long straights.

Version 1.1 featured an elongated wheel base, the maximum size allowed by green power.
Whilst designing the racer we had to consider material selection, focusing on minimising weight whilst maintaining strength, rigidity and buildability. For the bodywork we selected carbon fibre and for the chassis titanium tubing.
​
Carbon fibre and titanium are both characterised by being lightweight with high strength and rigidity. Typically these materials are relatively expensive, however as they are used on the Filton site we were able to recycle material used in the manufacturing process to keep costs low.
Design Development
To further develop the design a CAD model was created and a critical analysis carried out to identify areas for improvement.
The main things highlighted were the shape of the nose cone and the excessive length of the car, these points were rectified by shortening the overall wheelbase and making a wider nose which curved naturally with the rest of the body.
We also added some aerodynamic improvements such as a windscreen to push air over the driver and fairings on the wheels to reduce drag.

Aerodynamic Assessment
To get the most out of the power the electric motor produces we need to reduce drag to a minimum.
To measure the efficiency of our concept we used AutoCAD's flow simulator to calculate our aerodynamic drag.


The assessment showed that the concept design was creating significant vortices behind the car resulting in substantial aerodynamic drag.
Much of this was generated by the exposed driver and the upright driving position as well as the exposed wheels. Unfortunately due to the regulations governing Greenpower it was not possible to adapt the design to reduce the drag.
We therefore redesigned the whole bodywork to focus on a much lower driving position, and a body design which would push the air over the exposed driver, reducing the drag.
Evolved Design
For the improved design we drew inspiration from Le Mans cars with low profile bodies and wheel fairings. The rear wheels are encased within the body to reduce drag whilst the front wheels are exposed to allow them to turn.

Our new design incorporated a much lower driving position which allowed the car to have a significantly lower profile with improved weight distribution. We then reran the simulation to characterise the improvements made.
