Additive Manufacture
More commonly known as 3D printing, GKN is at the forefront of developing Additive manufacturing techniques for full scale industrial production with centres of excellence in the UK (Filton, Bristol), Sweden (Trollhättan) and the USA.
​
At Filton we have a range of:
​
-
EBM (Electron Beam Welding)
-
LPB (Laser Powder Bed)
-
SLS (Selective Laser Sintering)
-
FDM (Fused Deposition Modelling)

Advantages of AM
Additive manufacture has many benefits over traditional subtractive manufacture such as via CNC machines. In aerospace there are three key areas to consider when designing and manufacturing parts:
printers, these allow the creation of lightweight, innovative components in Titanium, Inconel and various plastics.
-
Weight - The lighter each part on the aircraft is the less fuel it will use to fly, reducing the cost for the airline and the passengers.
​
-
Time to manufacture - The longer a part takes to create the more expensive it is, this can effect the overall cost of the plane.
​
-
Waste - The more waste material produced when creating a component the less efficient it is. This increases the cost of the final aircraft and is also damaging to the environment.
​
In these key areas additive manufacture outperforms traditional methods significantly.
​
CNC machining works by starting with a forged piece of metal and machining away the excess to leave the component behind.
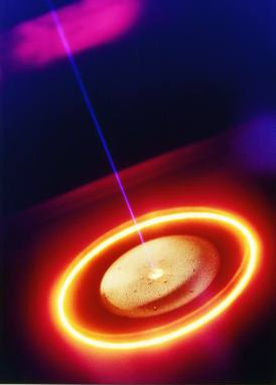
In comparison Additive Manufacture works by building the component up layer by layer, using only the material needed.
​
Components created using additive manufacture can be much lighter than their machined counterparts as they are built from the ground up rather than machined from a solid block.
Material is added only where necessary to give the component the required strength, this process is known as Topological Optimisation.
​
It has the effect of both reducing the weight of the component and its manufacturing time as less material translates to less time printing.
This is the opposite of CNC machining where reducing the weight of the component means more time spent on the machines, this is expensive and often results in a trade-off of a heavier component at a lower cost.
To support the rear axle (the car is rear wheel drive) we are using 4 bearing hangers attached to the titanium chassis. To save on weight these will be printed from Onyx (carbon fibre impregnated nylon) on a MarkForged Mark Two printer.
One of the newest printers in the Additive Manufacturing Centre this printer allows GKN engineers to print innovative components which incorporate strands of either carbon fibre or Kevlar.
​
By using this technology we will be able to reduce the weight we add to the car without compromising the quality of the components due to the strength and stiffness provided by the carbon fibre. In addition the MarkForged can be set to pause after a set number of layers, this will allow us to print half the of the hangers insert the bearings and then continue the build. This method will securely mesh the bearings into the part.
​
​
Courtesy of ARCAM





Traditional CNC Machined component, made from a solid block reulting in large amounts of waste
Additive Manufacture component with an inovative lightweight mesh to reduce comonent weight
A printed topologically optimised component. Material is only added where needed to make a strong lightweight part
A hybrid optimised and mesh component to maximise weight reductions and minimise material waste
Additive Manufacture in Greenpower
For the Greenpower challenge we have been to utilise the cutting technology available in the Additive Manufacturing Centre at Filton, Bristol.
This has allowed us to design unique parts to fit our car rather than using premade components. The ability to print our own bespoke parts allows us to optimise each to reduce the weight of the car. You can read about some of the 3D printed parts we are incorporating into our design below.
​

The rear wheels of our design are encased within the body work to reduce our aerodynamic drag, however while this will increase our efficiency it presents an added complication when it comes to manufacture.
We are using standard road bike wheels mounted on an axle, it will therefore be very difficult to remove the rear wheels whilst the bodywork is fitted in the event of a puncture.
​
Using additive manufacturing technology we can solve this problem by printing unique hubs which release from the axle side, allowing the wheels to be changed quickly.
We can also fit high end ceramic bearings in our bespoke hubs, this will reduce our rolling resistance at a reduced cost compared with purchasing expensive road bike wheels.


